Winterarbeit 2019 / 2020
Heute mal zuerst die schlechten Nachrichten 🙁
Der Sturm Sabrina der hier über viele Tage sein Unwesen trieb, hat nicht nur die erst im Herbst beschafften Planen so gealtert, dass sie schon wieder ersatzbedürftig sind, er hat auch meinen (von mir als) schönen (empfundenen) Portalkran, nicht nur einmal, da waren die Schäden noch mit einfachem Aufwand reparabel, sondern auch noch ein zweites Mal umgeworfen. - Danach war die Zerstörung so hoch, dass sich eine Reparatur bzw. ein wieder Aufbau nicht mehr gelohnt hätte.
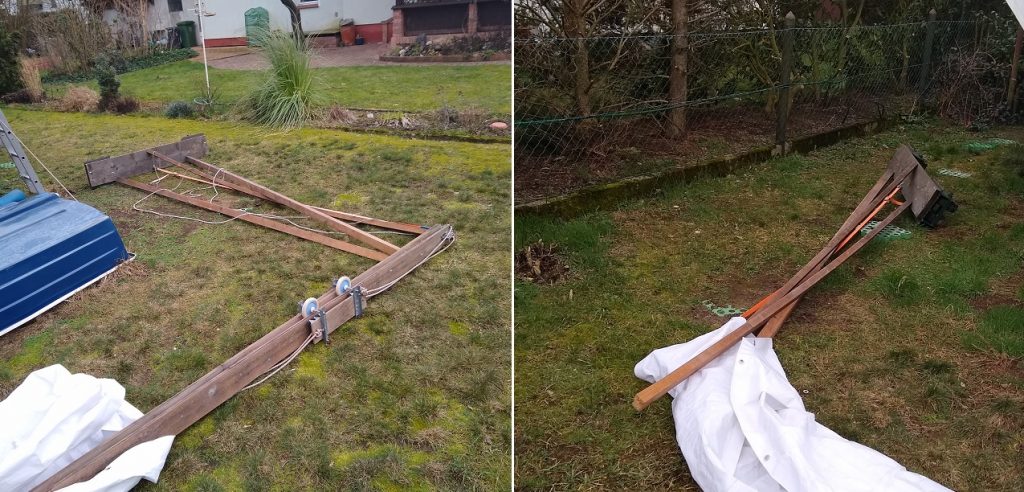
Das liegt auch daran, weil ich seit Januar meinen alten Metaller-Meisterbrief vor meinem inneren Auge vor die Stirn gepinnt habe und seither praktisch nur noch Stahlbleche und Rohre zersäge, bohre, feile, schleife und schweiße.
Vor 40 Jahren nämlich, trug es sich zu, dass ich mich nur dadurch legal von der Truppe entfernen konnte, indem ich mich der Industriemeister Metall Ausbildung hingab. Durchaus nicht unbedingt gewollt, aber zum Luftfahrtprüfer fehlte mir die notwendige Praxis(zeit), jedoch für den Meister reichte es(?)
Metall war nie meine Leidenschaft, braucht man dafür doch ziemlich besondere Bearbeitungswerkzeuge und viel Maschinenpower - damals für eine g'schaftelhuber Bastelwerkstatt eigentlich nicht wirklich sinnig, heißt, dem Taschengeld nich' nachhaltig zuträglich.
Aber seit die Chinesen kräftig mitmischen, hat sich bei den Kosten für Material und Werkzeuge doch einiges zum Vorteil, diesesmal für den Kunden, getan.
Nur das Biegen der Rohre habe ich den Profis überlassen, dafür habe ich keine Möglichkeiten.
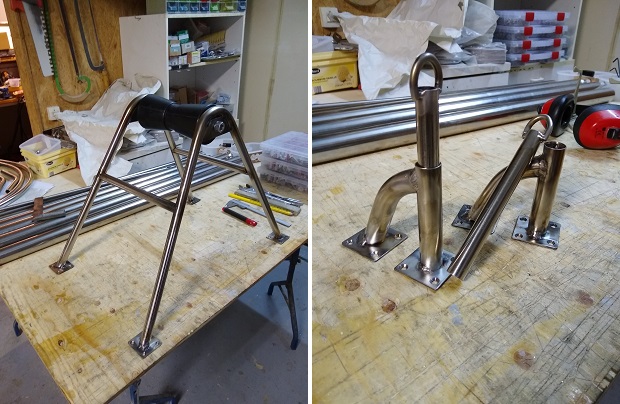
Mit der Konstruktion der Davits (Bordkran), sie stehen am Heck und dienen haupsächlich dazu das Dingi aus dem Wasser und andere Lasten an Deck zu heben, habe ich mich mal wieder weit aus dem Fenster gelehnt.
Wieder konnte ich meine Vorstellung über die Nutzungsbreite nicht so richtig im Zaum halten und habe den Ausleger so konstruiert, dass er um das 2,5 Fache teleskopartig ausgefahren werden kann.
Hier bin ich dann auch klar am anderen Ende des Masstabes meiner Möglichkeiten, was die Fertigung kleiner Teile in ausreichender Genauigkeit betrifft, angelangt.
Die beiden Davits stehen kurz vor der Vollendung, in voller Aktion also erst beim nächsten Beitrag.
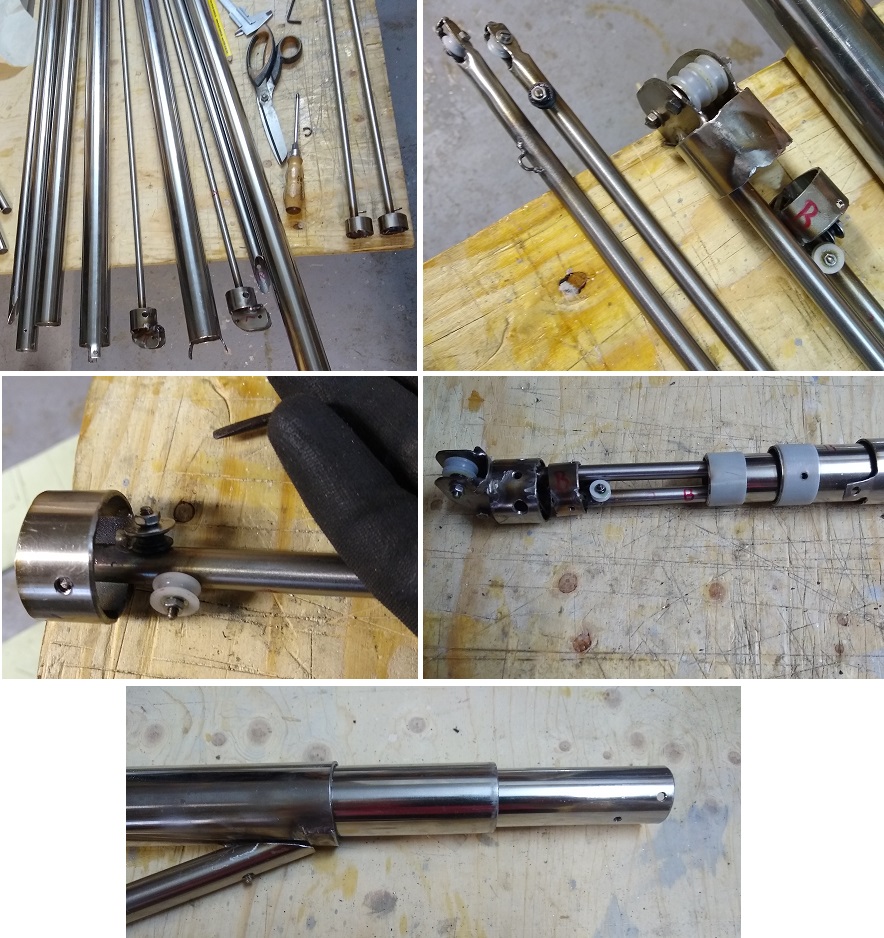
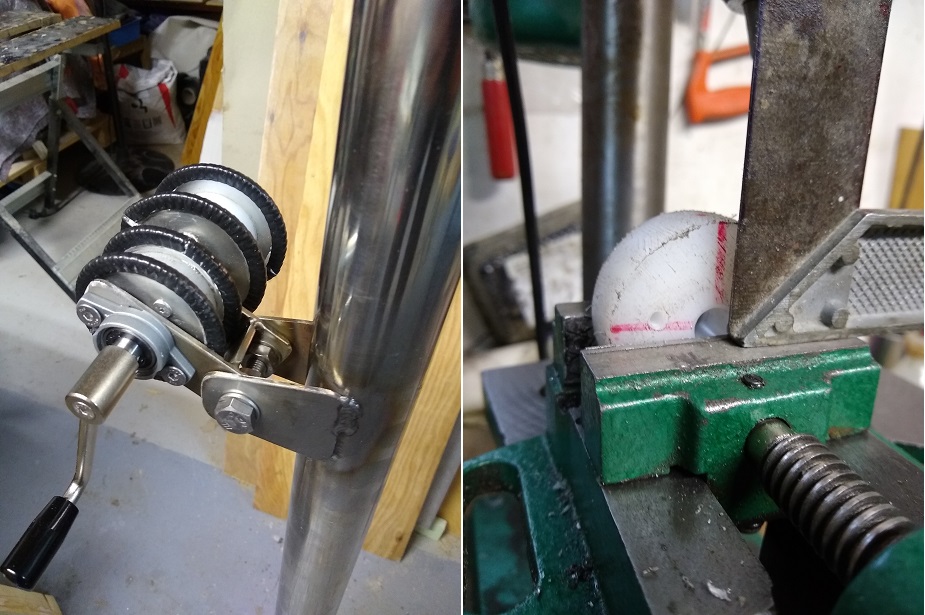
Nicht nur hier bin ich klar am Ende meiner Präzisionsmöglichkeiten, allem in allem ca. auf einen halben Millimeter genau, +- 2,5 Zehntel.
Es rudert wieder
Zunächst ging's mit Metallarbeiten weiter. Die beiden Davits sind nach mehreren Entwicklungsprozessen tatsächlich soweit fertig (Bilder, wenn sie eingebaut sind 😉 ).
Sehr zeitraubend waren die Umlenkrollensätze für die Seil- bzw. Leinenführung. Dabei geht es darum möglichst alle Steuerleinen des Riggs (der Besegelung) in das Cockpit hinein zu führen, damit das Boot später "trocken", also weitestgehend aus dem geschlossenen, besagten Cockpit heraus, gesegelt werden kann. Da kommt so einiges zusammen. Ganze 28 Leinen können vom (schrägen) Deck in das Cockpit geführt werden. Dort, wo es warm und trocken ist 🙂 , sind dann auch die Winchen, und was sonst so noch zur Leinenführung notwendig ist, eingebaut. Altersgerecht eben!
Hier war wieder, für meine Verhältnisse, Feinarbeit gefragt. Dagegen waren die Motorträger, für meine Verhältnisse, genau das Gegenteil. Genaugenommen bestimmen in diesem Fall "meine Verhältnisse" die Möglichkeiten meines Schweißgerätes - um die 2mm Blechstärke sind da die Untergrenze, um die 6mm die Obergrenze dessen was ich damit so schweißen kann, ohne mehr kaputt als gut zu machen.
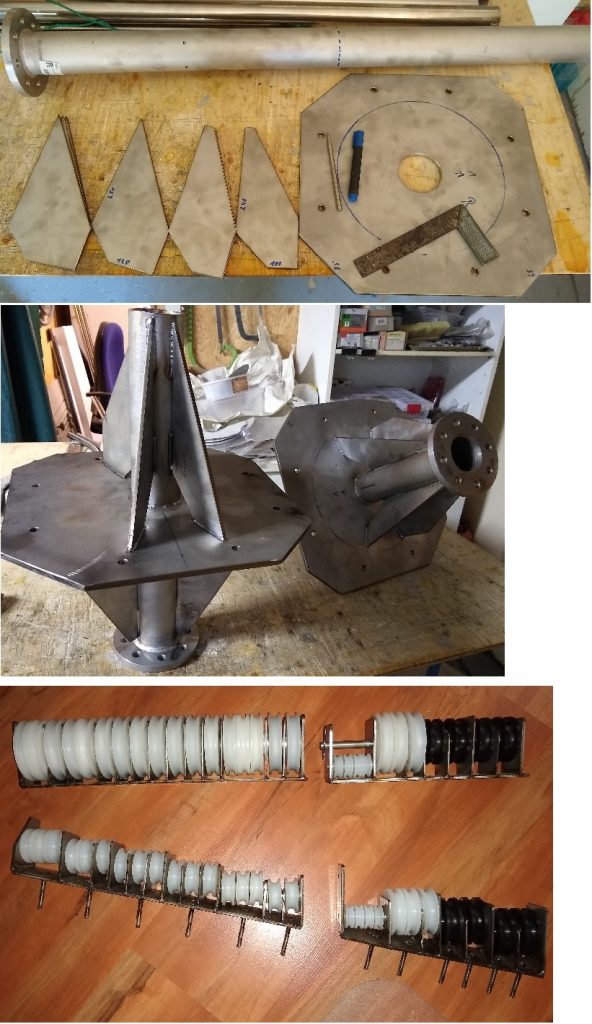
Mitte, die fertigen Motorträger mit allen eingeschweißten Verstärkungen.
Unten, die Umlenkrollensätze der Seil- bzw. Leinenführungen. Dem Absatz des Decks geschuldet in je zwei Abschnitten. Die jeweils unteren Umlenkrollensätze folgen der Schräge des Decks und lenken die Leinen nach oben, um sie dann über die oberen Umlenkrollen in das Cockpit hinein zu führen.
Die Motorträger (Adapter) mussten so gebaut werden, damit sie auf die "alten", sich im Boot befindliche Montagebetten passen, in denen die vorherige Motoren, bzw. das Getriebe, eingebaut waren.
Jetzt können die neuen Motoren am Boot befestigt werden, bei denen es sich ja um Elektromotoren handelt, die unter Wasser, an die beiden Flansche des im Bild zu sehenden Rohres verschraubt werden. Die Kabel werden dann durch die Rohre ins Bootinnere geführt. Und falls die Motoren selbst mal undicht werden sollten, ragen die Rohre bis über die Wasserlinie nach oben ins Bootinnere hinein.
Die erste Arbeit am Boot sollte die Rudersanierung werden. Aber wie aus bauen?? Sie stecken 75 cm tief von unten im Rumpf und da waren nur rund 15 cm Platz.
Erst wollte ich schon zwei Löcher buddeln, aber da kam mir der Gedanke, das Boot vielleicht so weit nach vorn kippen zu können, bis das Heck hoch genug steht um die Ruder frei nach unten ausbauen zu können.
Ich habe es x Mal gerechnet und maßstabsgerecht gezeichnet, wenn der Drehpunkt am vorderen Ende der Kielstümpfe lag, musste das Boot nur um 9° nach vorn gekippt werden, damit hinten genug Platz zum Ausbau sein würde, und das Boot noch nicht mit den Bugwülsten auf den Boden stoßen würde. Also die Wagenheber hervor geholt .....
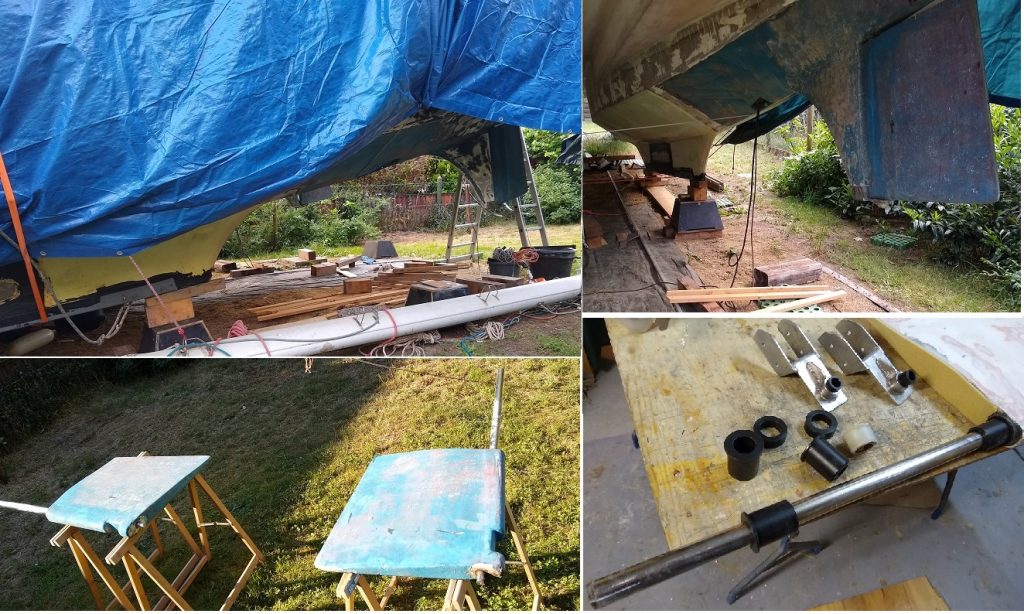
..... und schwupps - Ruder ausgebaut 🙂 . Unten rechts, die neuen Lagerbuchsen.
Und weil die Nase gerade so schön auf Arbeitshöhe ist, habe ich gleich den Bugbereich, besonders den üblen Schaden, repariert und saniert.
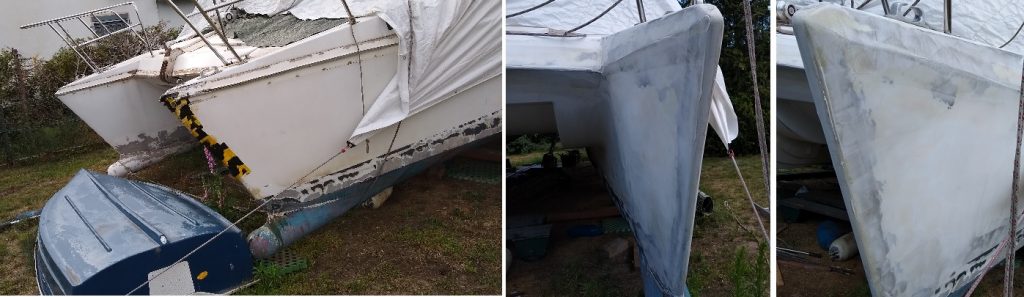
Aktuell werden die Ruder wieder eingebaut. Und weil auch das Heck gerade eine so schöne Arbeitshöhe bot, habe ich ebenfalls die Sanierung des hinteren Unterwasserbereichs soweit es ging voran getrieben.
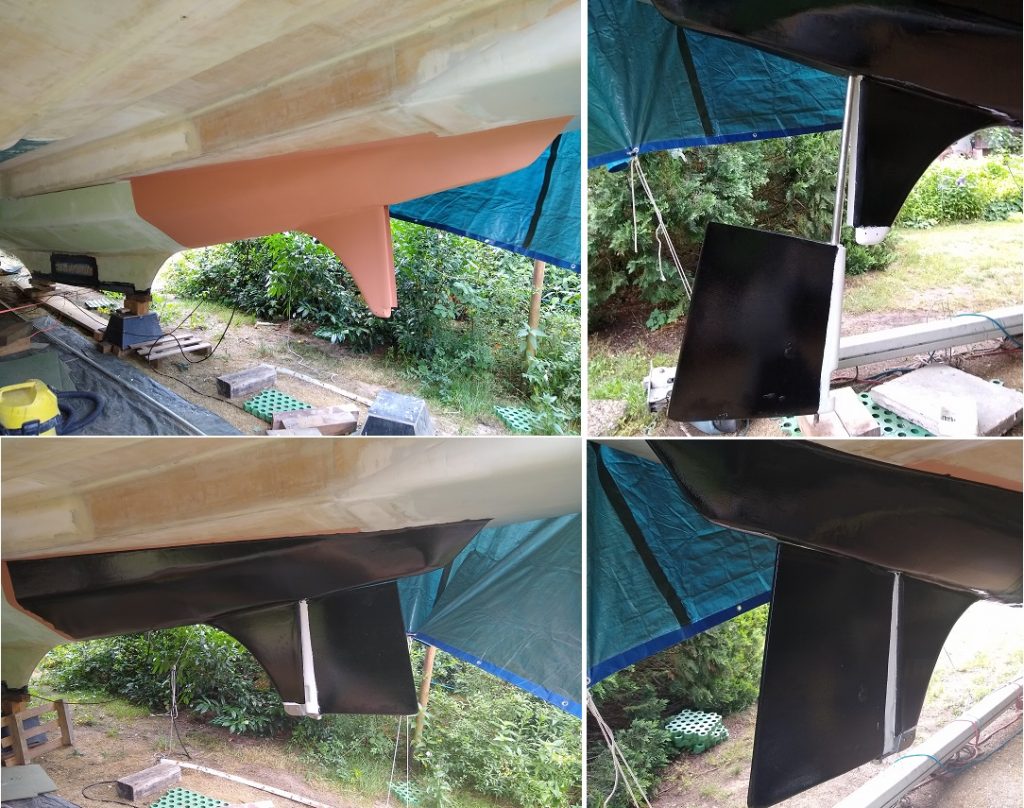
Die Ruder sind wieder eingebaut 🙂
Auch das Schwarz ist immer noch nicht die letzte Strophe. Frühestens 4 Wochen bevor der Rumpf wieder Wasser fühlen soll, kommt nochmals ein andersfarbiger Bewuchsschutz (Antifouling) auf das Unterwasserschiff.
…und dann war es passiert!
Um also wieder vernünftig am Boot arbeiten zu können musste es zurück in die Waagerechte. Und klar, natürlich so gut es geht "ins Wasser" gelegt werden, heißt, so waagerecht wie möglich neu ausgerichtet werden.
Alles schien bestens, der Bug sollte "nur" noch ca 17cm angehoben werden, damit auch die Konstruktionswasserlinie wieder waagerecht ist.
Dazu stand das Boot vorn, je rechts und links auf einem Wagenheber, womit es nach und nach, rechts drei vier Hübe, links drei vier Hübe hoch gehoben werden sollte.
Zuerst war es nur ein unscheinbares knacken beim Heben auf der rechten Seite - bis ich bemerkte, dass sich mit jedem Knacken das Boot ein ganz klein wenig mit dem Bug nach links drehte.
Das dies überhaupt möglich ist, liegt wohl hauptsächlich daran, dass der Verband des Katamarans so stark ist, dass der Hub nur einiger mm bei einem der vier Auflagepunkte gleich den ganzen Rumpf dieser Seite anhebt und damit, in diesem Fall, jeweils ein hinterer Auflagepunkt frei kommt, das Boot in diesen Momenten also nicht mehr auf vier, sondern nur noch auf drei Punkten aufliegt und der jeweilige hintere Auflagepunkt auf diese Art immer wieder zu einem Drehpunkt wird.
Das Unheil nimmt seinen Lauf - das Boot kann sich um den einen verbleibenden hinteren Auflagepunkt aus der Richtung drehen und tut es auch 🙁
Das Knacken wird immer schneller, "was tun", jetzt sehe ich erst wie sich die Wagenheber zur Seite neigen und erkenne was geschieht, ich entscheide die Linksdrehung des Bugs durch Heben der linken Seite aus zu gleichen, ein - zwei Hübe - ein riesen Knall und einen Stubs gegen meinen Rücken, das Boot ist von den Hebern gefallen!
Im Nachhinein, mit Zeit zum Nachdenken, war's dann wohl die exakt falsche Maßnahme!! Wie konnte ich nur so dilettantisch falsch entscheiden? - Indiziert doch der rechte Wagenheber mit seinem Hub eine Drehung nach links! Richtig wäre also gewesen den Wagenheber rechts wieder ab zu lassen, quasi mit einem Schlag wäre das Boot wieder auf vier Auflagepunkten gestanden und damit sofort ein Weiterdrehen verhindert worden, so hat der bereits nach links aus der Senkrechten stehende Heber den Dreheffekt wahrscheinlich eher verstärkt und ... ~ .
Bis auf den leichten Stoß durch den mittleren Pseudorumpf war mir nix passiert und auch das Boot hatte den Fall aus ca 25cm in den weichen Sandboden offenbar schadlos überstanden.
Leider hatte ich links neben dem linken Rumpf den Mast auf dem Boden liegend gelagert. Durch die Linksdrehung kam der Kielstumpf über den Mast, um dann von oben auf den Mast zu fallen, der hat's dann auch nich' überlebt.
Also doch nicht ohne Schaden!
Nach ein paar Tagen hatte ich einen (neuen) gebrauchten Mast in Greifswald gefunden.
Das Profil ist zu 99% identisch und obwohl am Originalmast kein Typenschild mehr vorhanden ist, um die Vergleichbarkeit der beiden Masten festzustellen, geht auch der Werftchef, der den gebrauchten Mast anbot, von einer Vergleichbarkeit aus. Der Mast gehörte zu einem größeren, jedoch praktisch gleichschweren Einrumpfboot und muss zudem für die EmilyStar um 4m gekürzt werden, um auf die Originalmasthöhe zu kommen.
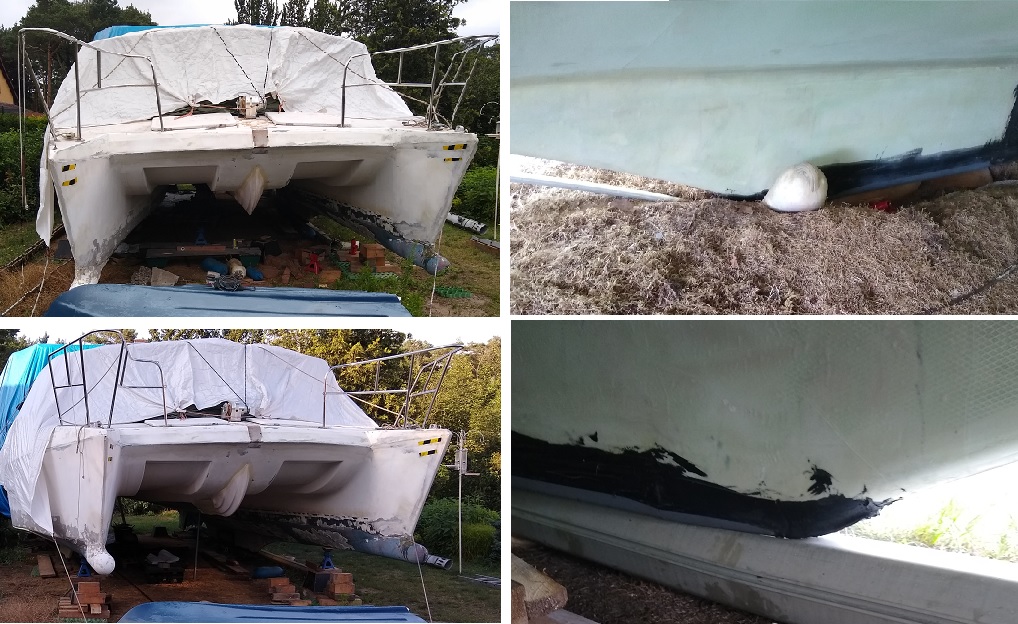
Bild2 und 4: Der rechte Rumpf steckt im Sand, der linke steht auf dem Mast, der deutlich verbogen wurde.
Bild3: Das Boot ist wieder ausgerichtet
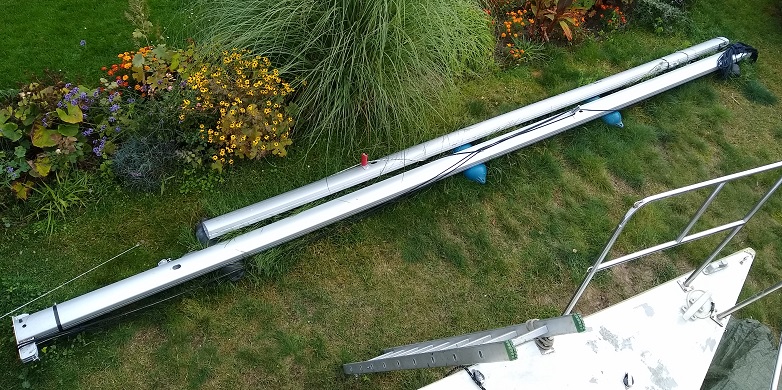
Alles in allem war der Preis weit weniger als die Hälfte wie für einen wirklich neuen Mast!
Ich war dieses Jahr bisher wirklich fleißig dabei!! Glaub' ich!
Da war Corona gerade recht. Das Freizeitangebot war so oder so stark eingeschränkt, also warum dann nicht an dieser Stelle ausnutzen.
Auch Hartmutens Urlaub fiel Corana zum Opfer, also hat er die Zähne zusammengebissen und hat "URLAUB" auf meiner Pseudowerft gebucht 🙂
Aber er hatte auch sein Motorrad dabei und die eine oder andere Fahrt haben wir zwischendurch machen können.
Hartmut ist ein Profi im Einmessen und Herstellen im idividuellen Holzausbau. Er arbeitet gut und gerne doppelt so schnell, als ich das kann und mit einer von mir starkt beneideten Professionalität beim Einmessen von wirklich kompizierten Bauteilen!!
Und so gab es in den 14 Tage seines "Urlaubes" auch einen richtigen Ruck.
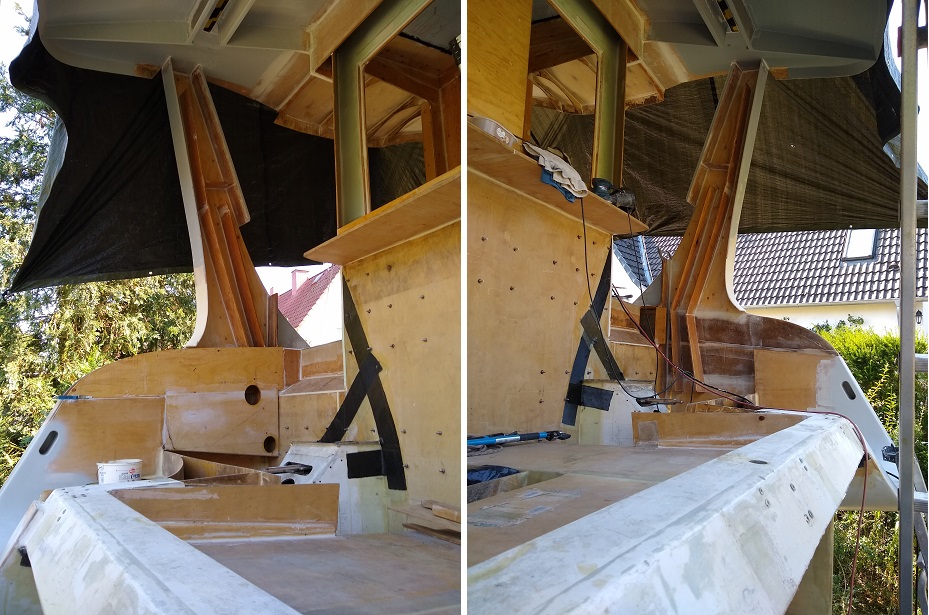
Bis dahin hatte ich die Isolation der Rümpfe fast fertiggestellt und den Ausbau im Heck voran getrieben. Die beiden vor produzierten noch fehlenden Spoiler, die doppelte Wandung, die zweite Stufe etc. hatte ich bereits eingebaut.
Schon Wochen vorher hatte ich angefangen exakte Detailpläne zu erstellen, so für das Cockpit-Segment, d.h. von unten angefangen mit den Einbaupositionen der Dieseltanks, den Duschraum, dem Wohnbereich II im linken Rumpfbereich und im mittleren Bereich bis zum Cockpitboden mit samt dem Segelsteuerstand, der als erstes benötigt wird.
Durch den Rohbau des Cockpits bis zum Boden ist der Einstig ins Boot erheblich erleichtert.
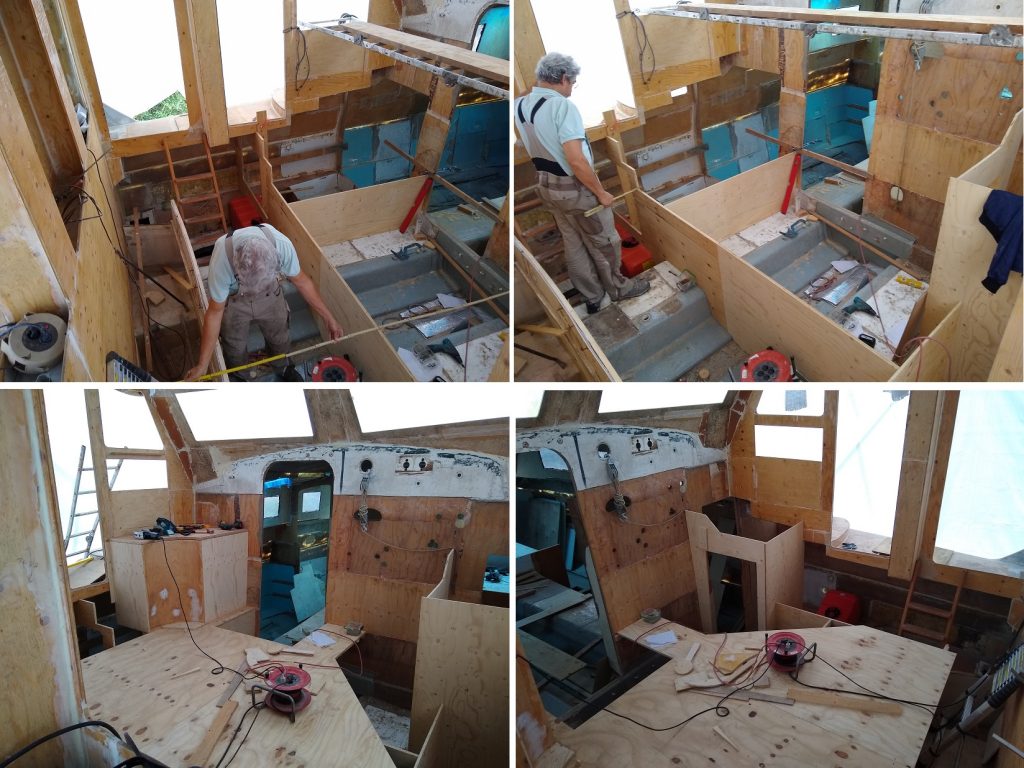
Es ist praktisch nur hineingestellt, passt also bereits alles auf +- wenige mm! Später muss ich alles wieder herausnehmen und von unten nach oben fest ins Boot ein laminieren.
Bild3: Der Boden ist schon mal drauf gelegt und der Segelsteuerstand ist zu erkennen.
Bild4: Die Umfassung der Duschkabine ist zu erkennen. Allerdings ist der offene Ausschnitt keine Tür sondern die Öffnung einer Serviceklappe in den davor liegenden offenen Bereich, der später unter dem dort erhabenen Boden des Fahrstandes verschwindet.
Bereits zusammen haben wir auch den Ausbau des Heckbereiches weiter voran getrieben.
Die seitlichen Aufstiege, sehr kompizierte Teilabschnitte, die zum Teil aus den Zugangsklappen zu den darunter liegenden Bereichen bestehen, die zum Beispiel die Ruderanlage enthalten, wurden bereits gemeinsam gebaut. Diese haben auch Hartmuts Mess- und Baukunst ordentlich gefordert.
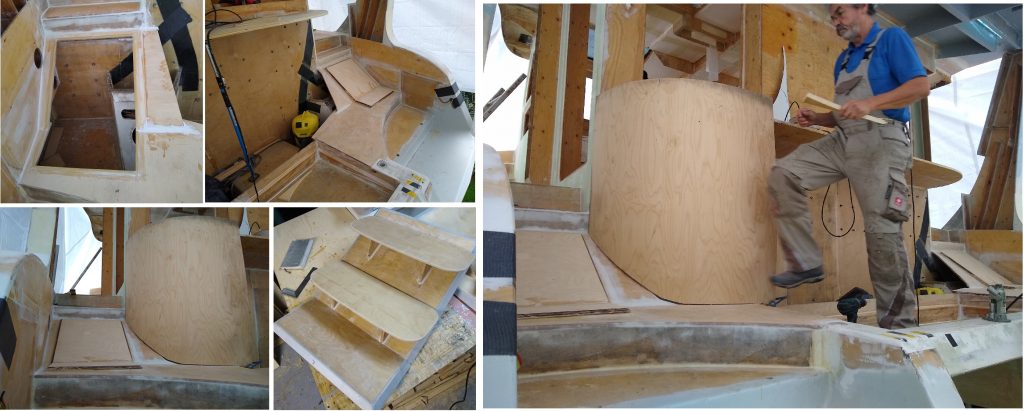
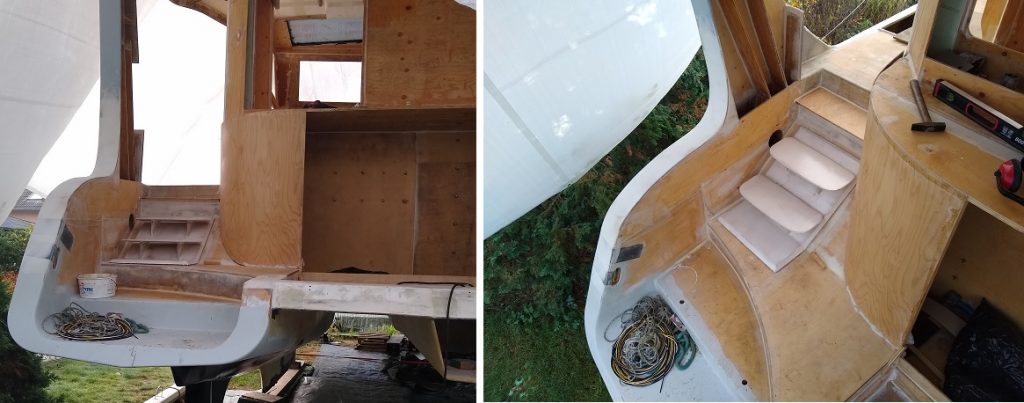
Stand der Dinge ist, die Rümpfe sind im Unterwasserbereich zur Hälfte und im Überwasserbereich fertig laminiert.
Bis auf vier Fenster sind alle festen Fenster und die Dachfenster im Cockpitdach eingeklebt.
Die Laminate im Überwasserbereich bekommen zur Zeit eine Schutzschicht (Gelcoat).
Da ich ein Epoxidharz habe, mit dem bis auf 5 ° C herunter gearbeitet werden kann, arbeite ich soweit ich komme auf die Lackierung des äußeren Bootkörpers hin.
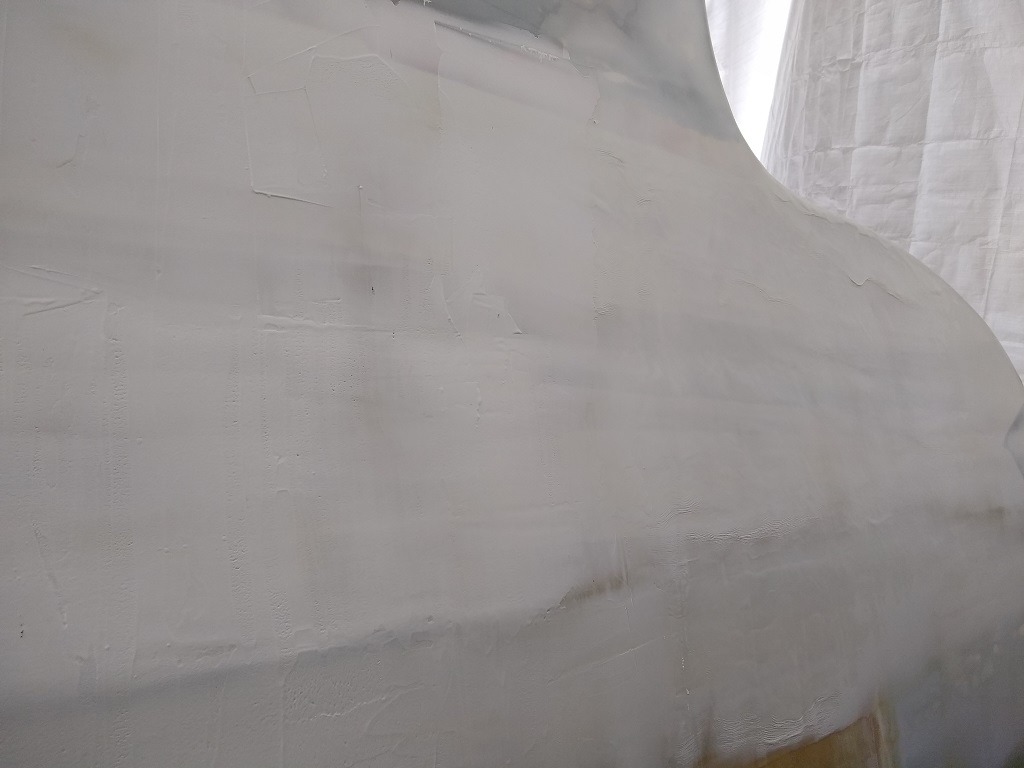
Unter zusätzlicher Zugabe von Kohlesäurepulver zu den drei sonstigen Ingredienzien, mit denen ich Spachtel und Pasten zusammen mit Epoxidharz herstellen kann, kann auch das Gelcoat selbst hergestellt werden. Durch das CO2 Pulver wird eine besonders kratzfeste Oberfläche erzeugt.
…zuletzt (…) dann doch!
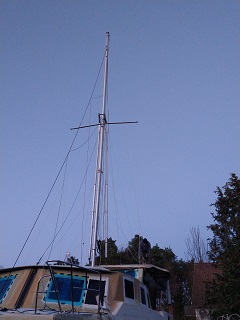
Das Wetter im Oktober ließ nicht mehr viel zu und so musste ich (wie jedes Jahr eigentlich) mich dem aufziehenden Winter geschlagen geben und die Arbeiten außen am Boot wieder praktisch einstellen.
Dies fällt mir jedesmal nicht leicht. Über die ganzen Jahre der Arbeit an dem Projekt gibt es mindestens zwei Mal diesen Bruch. Im Frühjahr, wenn die Arbeiten im Freien wieder möglich werden und im Herbst, wenn sie eingestellt werden müssen. Und jedesmal rüttelt es an meinem Inneren. Ich stecke noch mit allen meinen Gedanken und (Illusionen) Visionen in den aktuellen Arbeiten, sie sind schon tausend Mal fertig gedacht und kann sie wieder nicht vollenden, muss mich davon frei machen, alle roten Fäden abschneiden - es ist immer wieder ein Graus! Und ich brauche immerwieder Wochen um mich um zu stellen, die vor einem halben Jahr durchtrennten Fäden suchen, Bilanz ziehen, wieder aufnehmen, meine Visionen neu ausrichten.
Wer weiß, vielleicht hat das ja auch irgendwelche Vorteile, aber irgendwie lustig fühlt sich das nicht an.
Aber dieses Mal gab es ein erneut wichtiges Zwischenziel! Das neue Rigg!
Im letzten Herbst schon mal aktuell, und grandios in den Sand gesetzt (Siehe Beitrag: Der Mast stand ... fast 🙂 ) sollte es dieses Jahr werden.
Der Mast soll aufgestellt werden, damit die Segelmacher die neuen Segel aufmessen können.
Aber zuerst mussten ja alle An- und Umbauten, wie Einlaufrollen neue Position der Salinge (das sind die Querbalken, die der Stabilisierung des Mastes dienen) Maststufen, die Scharniere, das Einziehen der Fallen in den Mast etc., etc., durchgeführt werden - da war es schon weit über den halben November.
Als nächstes kam der Mastkran dran. Es mussten Anschläge für die Stabilisierungsleinen angebracht werden, und natürlich auch die Anschläge später dann für den Mast, vorbereitet werden.
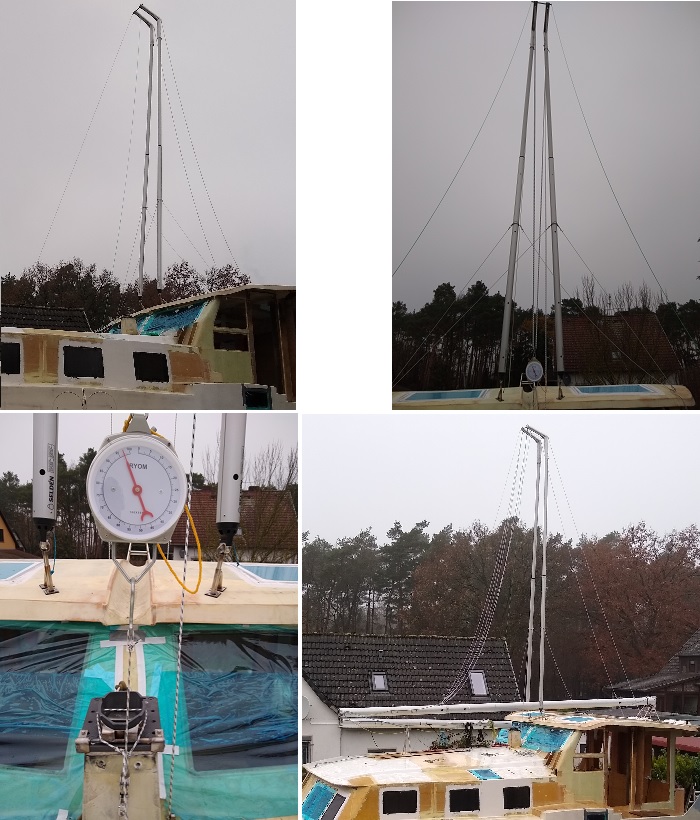
Dann wurde der Mast wieder auf's Boot gebracht und montiert. An dieser Stelle habe ich schon die ersten Zugversuche gemacht, auf der Jagt nach Schwachstellen oder gar Konstruktionsfehler die das Projekt insgesamt gestoppt hätten. Und es gab auch schlimmere Rückschläge. So wollte ich wissen wie groß denn nun wirklich die maximale Last am Kran ist. Also mal eben die Uhr nur mit einem S Haken dazwischen gehängt, der versagte natürlich und der Mast viel aufs Deck, nicht ohne Schaden an zu richten.

So ging es Tag um Tag, Stück um Stück einwenig weiter hoch, Schwachstellen finden, Kontruktion verbessern, viele viele Male.
Zuletzt noch alle Stabilisierungsleinen für den Mast anschlagen und --- das letzte Stückchen, es wollte nicht, wir mussten einfach zu viel Kraft aufbringen, mehr als wir sollten!
Ich habe an meiner Konstruktion gezweifelt, mich innerlich bereits angefangen damit ab zu finden, dass das Projekt gescheitert ist, gepaart mit der immer gegenwärtigen Angst, das ein Versagen eines Teiles, den Mast aus voller Höhe abstürzen lassen könnte.
Doch zuletzt waren es nur noch Seile die sich in jeder Position verhakten und ein weiter hoch auf die eine oder andere Weise verhinderten, bis kein unerwünschter Widerstand mehr da war und mit einem Mal, ganz leicht, völlig unspektakulär, klappte der Mast nach oben, stand senkrecht --- die ganze Hebelgeometrie tat was ihr angedacht war --- der Mast steht!!!
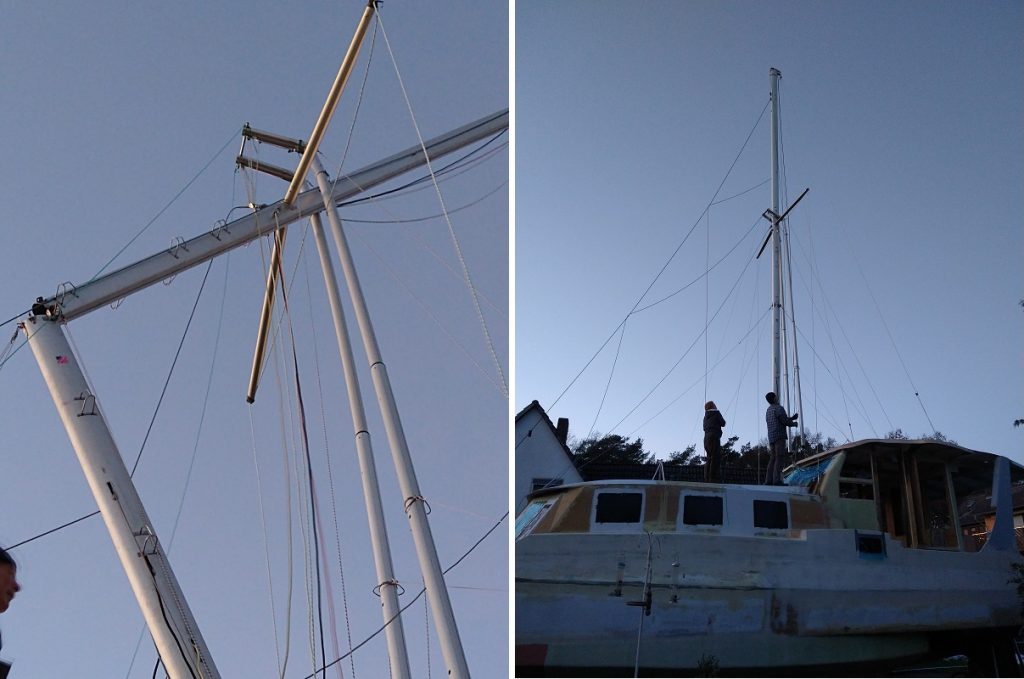